GreenLake wrote:OK. We'll be ready to hear them.
On an earlier question. You were wondering about a way to fold the cuddy door into the hatch. I'll want to see some kind of drawing of that, because while I can imagine the principle, I can't yet imagine how the door would fit - as I think it would tend to be wider than the opening, and therefore wider than the hatch.
Hi GL (et.al.)
I've know almost since the begining how I wanted to incorporate the cuddy door into the hatch assemby, it's just taken me this long to figure out how to draw it. Too complex (for me) to use sketchup and my hand drawing (as you see) leaves a great deal to be desired, but the idea sort of gelled for me in the last day, so I grabbed a pen, pad and business card straight edge and this is the fine result. I also apologize in advance as I'm doing this on my iPad and so I can't even cheat my way into a spell check.
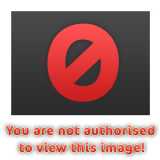
This is an old early picture (from a previous discussion) included only to provide context and frame of reference.
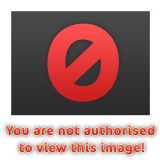
What you're looking at here would be a cross section from the back, with the companionway hatch up top, hovering "shoebox" style as you and Jay call it, over the raised lips of the edgetrim on the cuddy roof/deck.
My intent is to use a roller track (like a drawer track) attached to the movable cover of the companionway hatch with some vertical brackets.
Shown below the slide rails is the cuddy door (the normal vertical part) that has two pairs of rollers (counter-part to the slide rail) attached there-to.
If it's not obvious by the oh so clever dotted lines, the rollers go into the tracks and the cuddy door rides above the rails between the brackets.
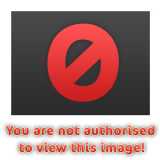
Rotate 90 degrees, now looking from the starboard side, showing pretty much the same setup, only in this view, the track is up attached to the hatch.
Ignore the bit at the bottom, that's part of the next picture.

So this is sort of where the rubber hits the road.
Top sketch shows the cuddy door parked up on the slide rails, both sets of wheels in the track.
2nd sketch shows the cuddy door pulled out partially, starting to tilt down hinging on the front rollers.
3rd sketch shows the cuddy door pretty much extracted, probably with a rail stop of some kind so it can't come all the way out, and notice the Companionway Hatch edge and the longer (top) portion of the cuddy door so when it comes down to the near vertical (closed position) the two surfaces will overlap to give some form of rain seal. At least that's the plan.
Not shown because I ran out of page, is the fact that the cuddy door will close against a finished edge extending from the inside of the cuddy, similar in concept to the top lip but flat (no L shape). The lip will be as wide as necessary so the door will cover the opening. Not sure if that makes sense to anyone but me.
So that's the plan. I'll run an edit/spell check on this when I'm back to my real computer later on.
Thoughts, comments, questions? Thanks - Scott
DS #6127 - Breakin' Wind - From the land of 10,000 lakes, which spend 80% of the year frozen it seems...